Technical excellence is one of our core values at CETEST. We look for continuous improvement in all our areas of expertise and testing means and capabilities. We are strongly committed to R&D projects as the tool for going further in our day to day work.
Some examples of latest R&D projects developed by CETEST
R&D Project SENSEROD
Soluciones de monitorización y diagnosis para gestión avanzada de los elementos clave del tren de rodadura de vehículos ferroviarios
CENTRO DE ENSAYOS Y ANÁLISIS CETEST, S.L. (CETEST) ha recibido una ayuda para su proyecto de Investigación y Desarrollo: SOLUCIONES DE MONITORIZACIÓN Y DIAGNOSIS PARA GESTIÓN AVANZADA DE LOS ELEMENTOS CLAVE DEL TREN DE RODADURA DE VEHÍCULOS FERROVIARIOS (SENSEROD), ayuda cofinanciada por la Unión Europea a través del Programa Operativo FEDER de Crecimiento Inteligente 2014-2020.
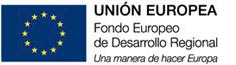

El proyecto SENSEROD se presenta con el objetivo de optimizar la gestión avanzada del tren de rodadura de vehículos ferroviarios, gracias al desarrollo de herramientas y soluciones de monitorización y diagnosis que permitan maximizar la vida útil y disponibilidad de los vehículos ferroviarios, así como incrementar su fiabilidad.
R&D Project TR4EMACS
This project has received funding from the Clean Sky 2 Joint Undertaking under the European Union’s Horizon 2020 research and innovation programme under grant agreement No 738110
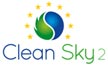
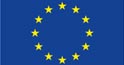
AIRBUS is the topic manager of this project, lead by CETEST with the collaboration of research centre IK4-CEIT. The aim of this project is the design, manufacture and power on of flexible and complete test rig for the on ground complete evaluation and validation of electromechanical actuators (EMA) and corresponding control units that will equip the control surfaces of the wings of the Clean Sky 2 Regional FTB2 demonstrator. The test rig will allow an on ground complete testing under realistic flight conditions in terms of mechanical performance, EMA control systems performance, EMA electrical consumption and its impact in the A/C electrical network.
TR4EMACS Article publication: “Modular and Flexible On-Ground Test Bench for Aircraft Electromechanical Actuators”
December 20th 2021
On the 20th of December 2021, the article titled: “Modular and Flexible On-Ground Test Bench for Aircraft Electromechanical Actuators” was published in the IEEE Aerospace and Electronic Systems Magazine. The authors are Iñaki Díaz, Eduardo Elizalde, Santiago R. López, Mikel Murga, Jorge Juan Gil, and it can be checked at the following link: Modular and Flexible On-Ground Test Bench for Aircraft Electromechanical Actuators | IEEE Journals & Magazine | IEEE Xplore.
The abstract is as follows: “Replacement of hydraulic actuators used in flight control surfaces by electromechanical systems is a current ongoing topic that targets higher performance in terms of efficiency, weight, maintenance, and pollution. While hydraulic actuators are already well-known systems for flight control surfaces, electromechanical actuators are still being developed and improved, and they have to be rigorously tested before they are used in the sky. Test benches used to analyze such systems are designed to be specific to the actuator being tested and lack correlation with other aircraft actuators. This work proposes a modular and flexible test rig architecture that allows different actuators to be tested alone or in combination so that all actuators of both wings may be analyzed together. Moreover, the proposed system allows the actuators to be tested by using dedicated power and control systems or by directly connecting them to the control bus bar and power source of a real aircraft. The test rig architecture and its components are described in detail and their application in new types of aileron and flap-tab electromechanical actuators explained”.
TR4EMACS Critical Design Review (CDR)– Step 02
December 2nd 2021
On Wednesday 2nd of December 2021 the Critical Design Review (CDR) meeting for both spoilers and winglet tab test rigs was successfully carried out. Personnel from different members composing TR4EMACS consortium were represented. CDR was virtually carried out.
During this meeting, requirements defined during the analysis of requirements task as well as all the actions considered on the PDR (Preliminary Design Review) were analyzed in detail in order to present the acquired solution.
After this meeting, the design was validated in order to begin the manufacturing of the test benches.
TR4EMACS Preliminary Design Review (PDR) – Step 02
October 6th 2021
On Wednesday 6th of October 2021 the Preliminary Design Review (PDR) meeting for both spoilers and winglet tab test was successfully carried out. Personnel from different members composing TR4EMACS consortium were represented.
Main points discussed were focused on the validation of different solutions for the test rigs mechanical design, control systems hardware and software in order to reach the requirements specified by the Topic Manager. After technical discussion, next project steps were planned. This meeting was telematically developed.
TR4EMACS Kick Off Meeting (KOM) – Step 02
September 1st 2021
On Wednesday 1st of September 2021, the Kick Off Meeting of the step 2 of the European project TR4EMACS (flexible test rigs of aircraft control surfaces powered by EMAs) was remotely carried out.
Researchers from different members composing TR4EMACS consortium (AIRBUS, CEIT and CETEST) met in this Kick off Meeting to draw up the project and to set up the work plan for the following months of research with the aim to design, manufacture and power on flexible test rigs for the on ground evaluation and validation of electromechanical actuators (EMAs) and corresponding control units that will equip the control surfaces for spoilers and winglet tab control surfaces of the wings of the Clean Sky 2 Regional FTB2 demonstrator.
TR4EMACS Power on and Customer Inspection at Purchaser Site (CIPS)
July 24th 2019
On Wednesday 24th of July 2019, the Ailerons and Flap-Tabs test benches were powered-on after integration at the Customer facilities. Previous to this step the Customer had carried out a thorough (CIPS) Inspection at Purchaser Site at their facilities. Personnel from different members composing TR4EMACS consortium were represented.
A thorough review was carried out by AIRBUS representatives and any adjustments required for the complete mechanical, electrical and hydraulic integration with their facilities was performed.
During this validation phase no major deviations were found and the test benches are currently fully operative.
TR4EMACS Customer Inspection at Supplier Site (CISS)
March 07th 2019
On Thursday 07th of March 2019, after completion of the Ailerons and Flap-Tabs test benches the Customer Inspection at Supplier Site (CISS) was successfully carried out at CETEST’s facilities in Beasain. Personnel from different members composing TR4EMACS consortium were represented.
A thorough review was carried out by AIRBUS representatives, including mechanical, electrical and hydraulic tests, as well as, a software and control review and performance tests.
During this validation phase no major deviations were found and the test benches were validated for delivery to the customer facilities for additional test and integration.
TR4EMACS Critical Design Review (CDR)
March 17th 2018
On Wednesday 17th of March 2018 the Critical Design Review (CDR) meeting for both ailerons and flap tab test rigs was successfully carried out. Personnel from different members composing TR4EMACS consortium were represented. CDR was carried out at AIRBUS facilities in Getafe.
During this meeting, requirements defined during the analysis of requirements task as well as all the actions considered on the PDR (Preliminary Design Review) were analyzed in detail in order to present the acquired solution.
After this meeting, the design was validated in order to begin the manufacturing of the test benches.
TR4EMACS Preliminary Design Review (PDR)
December 13th 2017
On Wednesday 13th of December 2017 the Preliminary Design Review (PDR) meeting for both ailerons and flap tab test rigs was successfully carried out. Personnel from different members composing TR4EMACS consortium were represented.
Main points discussed were focused on the validation of different solutions for the test rigs mechanical design, control systems hardware and software in order to reach the requirements specified by the Topic Manager. After technical discussion, next project steps were planned. This meeting was telematically developed.
TR4EMACS Kick Off Meeting (KOM)
September 13th 2017
On Wednesday 13th of September 2017, the Kick Off Meeting of the European project TR4EMACS (flexible test rigs of aircraft control surfaces powered by EMAs) took place at CETEST facilities (Spain) . Seven researchers from different members composing TR4EMACS consortium (AIRBUS, CEIT and CETEST) met in this Kick off Meeting to draw up the project and to set up the work plan for the following 42 months of research with the aim to design, manufacture and power on flexible test rigs for the on ground evaluation and validation of electromechanical actuators (EMAs) and corresponding control units that will equip the control surfaces of the wings of the Clean Sky 2 Regional FTB2 demonstrator. It lasted for one day, and every partners will be duly represented.
TEST-INN: INNOVATIVE LOAD APPLICATION & MONITORING SYSTEMS
This project has received funding from the Clean Sky 2 Joint Undertaking under the European Union’s Horizon 2020 research and innovation programme under grant agreement No-785393
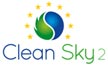
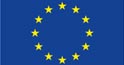
AERNNOVA is the topic manager of this project, led by technical center IK4-IKERLAN with the collaboration of CETEST. The aim of this project is to develop an advanced test rig in order to demonstrate the torsional and bending stiffness of new HLFC (Hybrid Laminar Flow Control) leading edge configurations.
TEST-inn will help to reduce product development time risks and costs thanks to the design and manufacture of a test rig equipped with a combination of state of the art load application system in combination with the innovative monitoring methods proposed for first damage detection, stress-strain events, overloads and hot spot detection and quantification as well as overall deformation measurement.
Thanks to the high level of adaptability and customization the new test rig configuration proposed, the project will contribute to speed up the development, not only of the new the HLFC testing prototype manufactured by the topic manager, but also of new products development time.